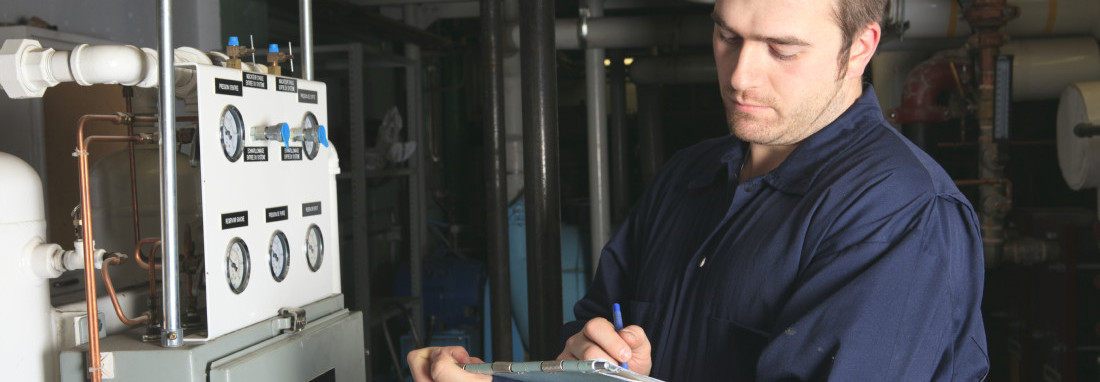
It’s well known that preventative maintenance can help keep your HVAC equipment performing at peak efficiency and extend the life of your system. But unexpected failures and problems do occur occasionally, and sacrificing staff in order to deal with these issues can be costly and time consuming. Here are some tips for creating a maintenance plan that incorporates both reactive and preventative maintenance strategies.
Strategize and Execute a Plan
One maintenance best practice is that reactive maintenance—responding to emergencies and unexpected situations—should only encompass about 15-20% of a technician’s total work. For some facilities this simply isn’t realistic, and the time spent on repairing reactive issues begins to creep higher.
Keep in mind that breakdown maintenance repairs cost 3-9 times more than planned repairs, so maintenance plans that rely heavily on reactive maintenance are generally the most expensive.
One strategy for dealing with this is to come up with a plan for how best to deal with reactive maintenance. You can assign one staff member to act as the reactive technician when a call comes in, and allow everyone else to stay on their pre-assigned PM work.
As Michael Crowley puts it, “If the repair history indicates that the facility averages 20-30 hours of reactive work per week, then only schedule the dedicated reactive technician 10-15 hours of planned work per week, knowing the rest of his or her week will be filled with the maintenance chaos that occurs daily.”
As you’re forming your plan, consider this: reactive maintenance should only be performed on components that are inexpensive, easy to replace, where failure does not cause collateral damage in the system.
You can also contract out either reactive work or preventative maintenance to an experienced HVAC contractor. This means that you have already budgeted specific time and money for either of these occurrences, and staff members who are already working on one problem won’t have to drop what they’re doing to start on something new.
Always Be Prepared
No matter your maintenance plan, be sure you are always prepared. This doesn’t just mean having the right tools on hand, but also any necessary parts, training, and transportation. Being prepared also means having a plan for who gets called and when. For example, in which cases should staff call in a mechanical contractor and when should they work to complete the job on their own? Having a firm process in place eliminates confusion and helps resolve the issue more quickly.
Planning for HVAC maintenance, whether it’s reactive or proactive, is all about balancing budget, workload, and strategy. With a little forethought and dividing time and money between both reactive and preventative maintenance, you can minimize downtime for your HVAC systems.
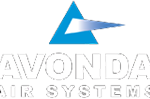
- Choosing an HVAC System When Building a New Home - September 21, 2015
- Mold in HVAC Systems: What You Need to Know - September 17, 2015
- Fall Vermont HVAC Checklist for Commercial Buildings - September 2, 2015
- What You Need to Know About Humidity in Your Vermont Home - August 25, 2015
- Does Your Office Have an Indoor Air Quality Problem? - August 10, 2015
- Stay Cool in Vermont with Ductless Air Conditioning - August 3, 2015
- 4 Things to Consider About Air Conditioning Replacement - July 27, 2015
- 3 Summer Ventilation Tips for Your Vermont Home - July 20, 2015
- Don’t Make These 3 Vermont Air Conditioning Mistakes This Summer - July 13, 2015
- When Should You Call a Vermont HVAC Contractor? - June 22, 2015